The Ware for September 2016 is shown below.
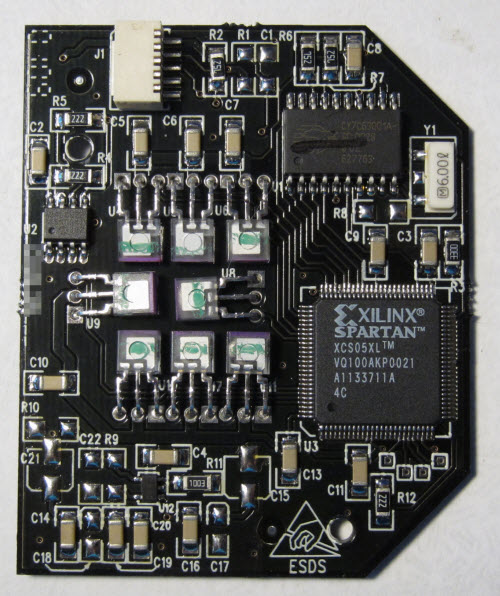
Thanks to J. Peterson for sharing this ware!
This entry was posted on Sunday, September 25th, 2016 at 5:45 pm and is filed under name that ware. You can follow any responses to this entry through the RSS 2.0 feed.
Both comments and pings are currently closed.
the photo diode arrangement reminds me of the one from a CD reader, it could be a similar beam detection device, just bigger.
As the “photo-diodes” are directly connected to the FPGA, they can’t have analog outputs. probably are light-sensors with frequency/pulse outputs, such as https://www.sparkfun.com/products/9768 and obviously there will be holes in the PCB.
The cypress part is a microcontroller with USB, so “J1” most ilkely has USB signals. CY7C63001A: “Low-cost solution for low-speed USB peripherals such as mouse, joystick, and gamepad”.
I’m sure that U2 is a i2c eeprom (such as the venerable 24cxx). Resistors towards the top are 2.2kOhm pullups on sda/scl. Not suitable to store the FPGA configuration, though. So this is probably done by the microcontroller via USB.
EEPROM is likely storing the CY7C63001A configuration – USB VID/PID, descriptors, etc.
At first, I thought it looked like the control board for a joystick. The stick would move a reflector or light so that each of the photodiodes received different intensity and then the logic elements would output that as a USB signal.
The only problem with that thought is that this board would be only for a joystick. No triggers or any other buttons as I don’t see any other connections for buttons on this board, and I’m assuming it’s a single-sided assembly since no other photos were posted.
But now, I’m thinking that not all joysticks applications need triggers.
My guess is that this is for some kind of joystick control without triggers. Like used on arcade machines or industrial controls.
Christian Vogel’s analysis is pretty thorough and seems spot on, not sure I can add much there.
I’d guess that this is one of those devices that plugs into a computer (via USB) and is used to calibrate the colors in a monitor. The other side would have filters over the cutouts for each of the light sensors. Their signals would then go to the FPGA which would do a bit of signal processing (changing the frequency values to light intensity values), then pipe that over USB to the computer to allow their calibration software to work its magic.
I like the color calibration angle. Looking at the housings of contemporary calibrators, it looks like the X-Rite Eye-One Display 2 calibrator has about the right shape. The overall shape is more of a pear, so I can imagine this board sitting in the lower half of this housing, and J1 feeding the USB cable that exits at the top end of the housing as it hangs in front of a monitor. There is a picture of the business end of the device on this page.
http://www.xbitlabs.com/articles/monitors/display/samsung-sm-xl24-xl30_7.html
I’m vague on how the optics might work, but I can imagine another lense sitting between the housing and this board.
Now I’m thinking that’s not quite it. Here’s a video teardown of an HP Eye-One device that looks like a relabeled version of the same device.
https://www.youtube.com/watch?v=JsU92-EzURQ
At around 9:00 the sensors are exposed and there are four sensors on a distinctly different circuit board. Lots of good hints in there though.
My first thought was also color calibration. And indeed it seems to be a Spyder 2 from Datacolor. The PCB on this site however looks rather similar:
http://richnelson.me/side-project/2016/02/21/Spyder-Colorimeter-Redesign-Concept.html
Nice! That looks pretty much spot on!
Wonderful! Congrats to North-X, that has to be it. I had located an exploded view of the Datacolor Spyder 3 here
http://designdesignonline.com/product/datacolor_spyder3.html
and it shows a different shaped circuit board and a seven element sensor in a different pattern.
I wonder how they use the multiple sensors. Four elements might give R, G, B and unfiltered intensity. North-X’s find shows 7 sensors, like the current Spyder line. We can see hints of a range of hues on the filters. Current marketing from Datacolor describes a “patented, full-spectrum 7-color sensor”. Our reference photo shows 8 sensors, maybe it’s a prototype.
One can easily tell it has light sensors, a USB controller and an FPGA.
What really gets me here is what could possibly warrant the use of an FPGA?
Assuming that the photo-diodes are similar to the ones on Sparkfun (thanks Christian Vogel), they each output frequencies between 200-300 KHz. That’s not too difficult to use with a regular micro-controller so the application must be doing some heavy signal processing.
The USB controller probably means this is a consumer facing device.
What does heavy signal processing with light for consumers?
My first guess is that this is a receiver from a LiFi device.
http://purelifi.com/lifi-products/lifi-x/
LiFi-X is full duplex so if this is correct then there would also have to be a board for transmitting light.
> What really gets me here is what could possibly warrant the use of an FPGA?
> output frequencies between 200-300 KHz
> That’s not too difficult to use with a regular micro-controller
You are overestimating the capabilities of cheap microcontrollers. If you do it in software, worst case you’ll have a interrupt rate of 1MHz. So you’d need 8 hardware timers for this (probably one more, as a timebase for when to sample the counts), with external inputs. I don’t even think there are any controllers available that have that many, certainly no cheap ones.
The old Spartan FPGA will cost you <$10 and the cheap low-speed USB probably goes for $1 in larger quantities. And you can very easily put counters in it.
One way to speed things up with microcontrollers is to not use interrupts but to use polling instead. In my experience, interrupts are often too slow (entering the interrupt, pushing everything on the stack, finding out which interrupt happened, exiting the interrupt again, …) and doing it with polling instead speeds it up. I once rewrote a firmware for a small microcontroller that was a bit too slow and unstable from interrupt to polling, and the rewritten software was fast enough and perfectly stable.
Originally I thought this receiver unit could have been mounted on a moving device (eg aimable receiver), but this seems unlikely due to some physical limitations. Conors’ idea of if being a light-comms device seems good.
There’s only two mounting holes on this board and you cannot physically put a screw in the top-left one. This leaves us with a couple of different mounting options I can think of:
– Plastic standoffs that click through the holes
– Clamping the board in a plastic case with little spikes that align in the holes
Neither of these options make it easy to keep the board extremely stationary when you are subjecting it to vibration. You’d rather just use screws instead.
The phototransistors do not appear to be glued down. If they’re just hanging by their legs then we can’t be doing anything involving high-speed vibration to this board, but given the physical spacing of each sensor I’d hazard that this was unlikely anyways.
I have a suspicion that the phototransistors are facing away from us, pointing instead into holes drilled in the PCB. You can see green marker marks on our side of each PT, which would be a bit flimsy if this is the optical side. We can also only see the metal baseplate in each PT (not the silicon die or any bond wires), so presumably the sensors are on the other side. It would be interesting to see what’s on the other side of the board.
I was hoping that the IC at the top-right would be a motor driver (and the header near it for a motor), but it turns out to be a USB controller. That’s a bummer. But the presence of USB does suggest that this is designed for something with traditional-computer (not microcontroller) scale number crunching, such as lifi internet. Otherwise USB would be inconvenient.
If it is an aiming feedback system for light comms then this is definitely on the fixed end (eg the laser itself is instead steered/corrected). I’d probably not design this to be mounted on something that moves/pans without either clamping it down, adding more screw-holes or gluing it to death.
Some final notes:
– Black silkscreen: less reflective. Perhaps to avoid ghost reflections in the case getting picked up by the PTs?
– Board shape. Why the two missing corners? Possibly in a small stylised plastic case?
Some evidence that this board is not for just aiming, but actually handles some of the high-speed comms itself:
1) The massive amount of ceramic decoupling for the PTs. Notably some larger/slower SMD caps are missing, they probably found out that they didn’t need them.
2) Each PT connects directly to the FPGA.
Perhaps it has to decode certain test signals? It seems like a very expensive way of doing it when you just instead slow down your laser pulsing. The USB micro is probably too much of a bottleneck for any serious data transfer speeds (although this might not need to be a super-duper-high-speed product).
Not sure what the 8-pin package is for (I can’t read its part number). It has no crystal and only a single decoupling cap, so it’s probably a simple part (eg op-amp, comparator, tranny array). It could also be flash/mem for either the USB micro or the FPGA, assuming that the board dimensions/layout restrictions meant they had to put it on a distant corner of the board.
A color calibration system (XRite i guess)
The optical sensors, the shape of the board and the use of the usb controller CY7C63001A leads to an optical mouse. The 8 sensors and the FPGA are used to track the direction of movement.
I guess this is a board from an optical mouse.
Optical mouse seems like a good guess but I have one concern — aren’t there optical sensor ICs just for this purpose? It would be cheaper and more practical than using 8 photo-diodes and an FPGA. Maybe this could be older than optical sensor ICs. Anyone know how old these parts are?
An optical rotary encoder. Perhaps the code is complex and the code disk is spinning fast thus justifying an FPGA.
The Cypress CY7C63001A in the upper right area is a USB Microprocess for USB 1.1, offering 1.5Mbps. The USB lane is routed to the connector U1 in the upper left area, so the whole thing is a part of a USB device that is put into a case, and a USB cable with a USB-A connector on the other side is connected inside the case directly to the U1 connector. One usual application for the CY7C63001A was being part of a computer mouse, Cypress still offers to send the required firmware for that application on request.
The controller is then connected to the Xilinx FPGA with several data pins, and the FPGA is connected to 8 interesting looking things that remind me of light sensors. 8 is a power of 2, so some kind of grey code detection would be a plausible application.
The 4 white labelled pins right next to R12 seem to be a JTAG port for programming the FPGA.
The Date-Codes are most likely 0028 and 0021, so it was produced in 2000. USB 1.1 was published in 1998, USB 2.0 was published in 2000, but products for USB 2.0 came on the market in 2002. So that looks plausible.
The light sensors are very similar to this component:
https://www.sparkfun.com/products/9768
It “… outputs a square wave (50% duty cycle) with frequency directly proportional to light intensity (irradiance)”.
So we have USB device that provides 8 light intensity sensors.
a bunch of photodiodes connected to an FPGA, It could be a receiver for a scanning laser tracker, similar to that concept :
http://www.hizook.com/blog/2015/05/17/valves-lighthouse-tracking-system-may-be-big-news-robotics
It’s a controller board for a breadmaker.
That’s a wild computer hardware guess.
This pcb could be an IMU unit from a laser scanning drone. Except from laser scanning, a LIDAR is using different type of light detection for different purposes. This could be a module of a LIDAR
Logic level out photodetectors. Kind of like (but not the same as) OPL530-OC
I wouldn’t think there isn’t much resolution in the device for super fancy optical work..
My guess would be something like a bar code scanner. Three lines for three bar codes, the photodetectors signal asynchronously to the FPGA and multiple detectors per line gives some error correction.
Just what Y1 is (it looks an awful lot like a Panasonic SMT relay) I’m still puzzling over.
My guess would be a barcode scanner, as the shape of the board and placement of the photodiodes suggests.
as the shape of the board and placement of the photodiodes suggests.
I’m hoping it’s the logic board out of a modern version of the Reliant logo turtle.
A color calibration system (XRite i guess)